Unleashing the Potential of Keo Tools: A Comprehensive Exploration
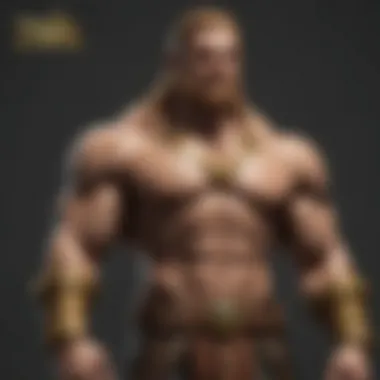
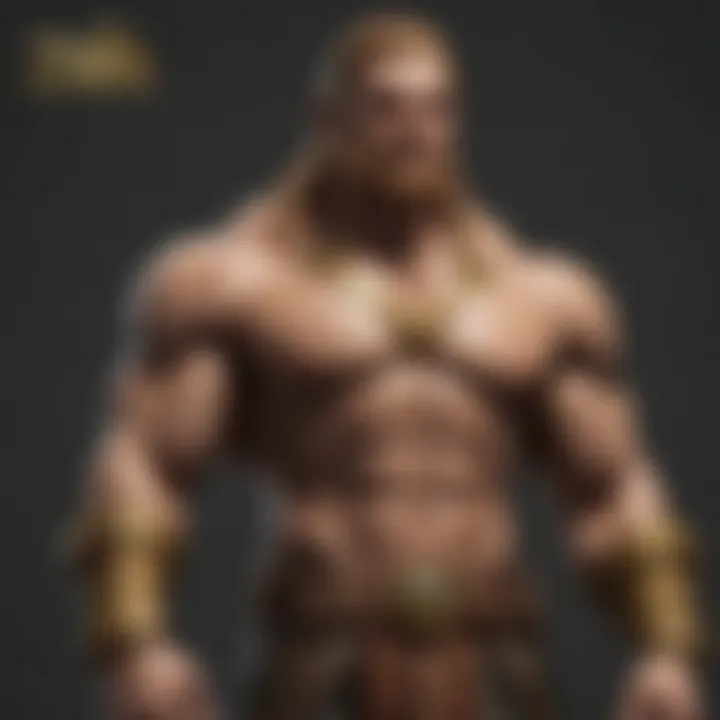
Game Reviews
Gameplay Features and Mechanics
Keo tools are renowned for their impeccable craftsmanship and precision engineering, setting a high standard in the industry. The attention to detail in the design of these tools ensures optimal performance and efficiency in various applications. From the intricacies of milling cutters to the finesse of countersinks, each tool is a testament to Keo's commitment to excellence.
Storyline and Quests
The evolution of Keo tools' lineup can be likened to an epic quest, with each tool representing a crucial chapter in the narrative of precision engineering. Delve into the backstory behind these tools, unraveling the intertwined threads of innovation and functionality that shape their journey through the industrial landscape.
Visuals and Sound Design
While Keo tools may not emit literal sounds or boast flamboyant visuals, their visual appeal lies in the sleek lines and finely crafted edges that define their aesthetic. The symphony of precision and durability resonates visually, speaking volumes about the quality embedded in every tool design.
Comparison with Previous Titles
Comparing Keo tools to their predecessors is akin to comparing a masterful sequel to its groundbreaking original. The advancements, refinements, and enhancements in each new iteration of Keo tools demonstrate a dedication to surpassing past achievements and setting new benchmarks in the industry.
Introduction to Keo Tools
Keo Tools are at the forefront of precision engineering, offering cutting-edge solutions that revolutionize various industries. In this comprehensive guide, we will delve into the intricacies of Keo Tools, highlighting their significance and impact on enhancing efficiency and accuracy across different sectors. Through an in-depth exploration of Keo Tools, readers will gain a profound understanding of how these tools are reshaping the landscape of modern engineering.
Understanding the Significance of Keo Tools
The Evolution of Keo Tools
The Evolution of Keo Tools represents a pivotal advancement in tool technology, showcasing the progression from traditional tools to state-of-the-art precision instruments. This evolution has been instrumental in meeting the increasing demands for high-quality performance and reliability in industrial applications. The incorporation of advanced materials and cutting-edge design features sets The Evolution of Keo Tools apart, making them a preferred choice for industries seeking optimum cutting solutions.
The Philosophy Behind Keo Tools
The Philosophy Behind Keo Tools embodies a commitment to excellence and innovation, underpinning the design and manufacture of these exceptional tools. With a focus on quality, durability, and performance, this philosophy drives the continuous improvement and customization options available with Keo Tools. Offering a blend of expertise and technological prowess, The Philosophy Behind Keo Tools ensures that each tool is not just a cutting implement but a precision instrument crafted to exceed expectations in diverse operational environments.
Applications of Keo Tools
Industrial Sectors
Keo Tools find extensive applications across various industrial sectors, catering to the diverse needs of manufacturing, fabrication, and production facilities. By delivering unparalleled precision and efficiency, Keo Tools have become indispensable in industries where quality and reliability are paramount. Their exceptional performance in demanding environments establishes industrial sectors as the ideal domain for the application of Keo Tools.
Manufacturing Processes
In manufacturing processes, the use of Keo Tools streamlines production operations, facilitating the creation of intricate components with utmost accuracy and consistency. The advanced features integrated into Keo Tools enhance the precision and speed of manufacturing processes, optimizing workflow efficiencies and improving overall productivity. By selecting Keo Tools for manufacturing needs, industries can achieve superior results, reducing wastage and maximizing output.
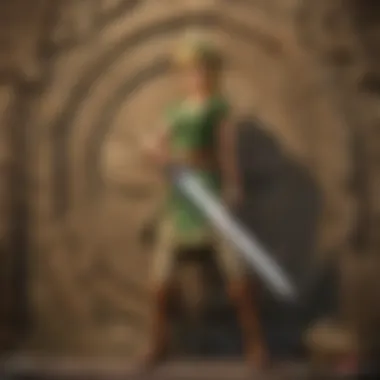
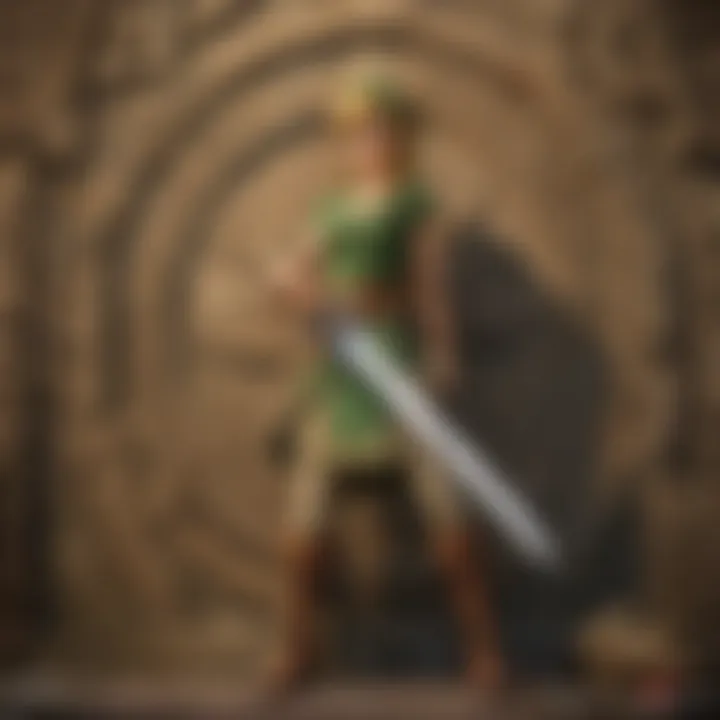
Engineering Fields
For engineering fields, Keo Tools offer a comprehensive suite of solutions tailored to meet the specific challenges of design, construction, and maintenance tasks. Whether in aerospace, automotive, or structural engineering, the versatility and adaptability of Keo Tools make them indispensable for precision machining and cutting applications. The reliability and durability of Keo Tools ensure that they are a trusted companion for engineers seeking superior performance and exceptional results in their projects.
Exploring Keo Tool Categories
In this section, we delve into the crucial aspect of Keo Tool Categories, shedding light on their significance within the broader context of this comprehensive guide. Understanding the categorization of Keo tools is fundamental as it paves the way for a more nuanced exploration of their applications and benefits. By dissecting the various tool categories, we can discern the specific functionalities and advantages attributed to each, offering invaluable insights into their suitability across different industries and processes.
Milling Cutters
End Mills
End Mills represent a pivotal component within the realm of Keo tools, characterized by their precision and effectiveness in milling operations. These tools boast a distinctive design that enables meticulous material removal and shaping, making them indispensable in various machining tasks. The key characteristic of End Mills lies in their versatility, allowing for a wide array of cutting applications with exceptional accuracy and surface finish. End Mills are highly favored for their ability to address intricate milling needs efficiently, making them a popular choice for professionals seeking optimal performance and reliability. Additionally, the unique feature of End Mills lies in their capacity to engage with different materials effectively, showcasing a balance between machining speed and precision that is unmatched in this article.
Solid Carbide Tools
Solid Carbide Tools stand out for their robustness and longevity, contributing significantly to the overall efficacy of Keo tools. These tools are renowned for their exceptional hardness and wear resistance, ensuring prolonged durability and consistent performance in demanding machining environments. The key characteristic of Solid Carbide Tools revolves around their ability to maintain sharp cutting edges throughout extended use, resulting in superior machining outcomes and minimized tool wear. Solid Carbide Tools are a preferred choice in this article due to their remarkable strength and cutting efficiency, making them a crucial asset for achieving high precision and productivity in various applications. Moreover, the unique feature of Solid Carbide Tools lies in their resilience to extreme conditions, offering a reliable solution for challenging machining tasks.
High-Speed Steel Cutters
High-Speed Steel Cutters play a vital role in enhancing machining operations with their exceptional speed and durability. These cutters are engineered from high-quality steel alloy, providing a perfect balance between toughness and cutting performance. The key characteristic of High-Speed Steel Cutters lies in their capability to withstand high cutting speeds while maintaining sharp edges, resulting in swift material removal and efficient chip evacuation. High-Speed Steel Cutters are a popular choice in this article due to their versatility and cost-effectiveness, offering a practical solution for a wide range of cutting applications. Furthermore, the unique feature of High-Speed Steel Cutters lies in their adaptability to various machining conditions, ensuring optimal results across different materials and cutting scenarios.
Countersinks and Counterbores
Single Flute Countersinks
Single Flute Countersinks play a pivotal role in deburring and chamfering operations, enhancing the precision and functionality of Keo tools. These countersinks feature a single cutting flute that excels in creating smooth and tapered holes with precise angles, making them ideal for achieving seamless finishes in metalworking tasks. The key characteristic of Single Flute Countersinks lies in their efficiency in creating uniform chamfers and countersinks, ensuring consistent results with minimal effort. Single Flute Countersinks are a beneficial choice for this article due to their ease of use and versatility, catering to a wide range of deburring requirements across different industries. Additionally, the unique feature of Single Flute Countersinks lies in their ability to enhance workflow efficiency and surface quality, offering a valuable solution for achieving refined machining outcomes.
Multi-Flute Counterbores
Multi-Flute Counterbores play a significant role in countersinking and counterboring applications, enriching the diversity and effectiveness of Keo tools. These counterbores feature multiple cutting flutes that excel in creating precise recesses and through-holes, facilitating efficient fastening and component assembly. The key characteristic of Multi-Flute Counterbores lies in their capacity to produce accurate and concentric bores with optimal chip removal, ensuring seamless integration of fasteners and fittings. Multi-Flute Counterbores are a popular choice for this article due to their versatility and precision, addressing a wide spectrum of counterboring needs with maximum accuracy. Moreover, the unique feature of Multi-Flute Counterbores lies in their ability to streamline assembly processes and improve hole quality, offering a reliable solution for achieving enhanced part functionality and fit.
Combined CountersinkCounterbore Sets
Combined CountersinkCounterbore Sets offer a comprehensive solution for applications requiring both countersinking and counterboring operations, elevating the efficiency and convenience of Keo tools. These sets encompass a range of tools that combine the functionalities of countersinks and counterbores, providing a complete machining solution for achieving accurate hole profiles and fastener recesses. The key characteristic of Combined CountersinkCounterbore Sets lies in their versatility and time-saving benefits, allowing users to execute multiple machining tasks with a single set of tools. Combined CountersinkCounterbore Sets are a beneficial choice for this article due to their all-in-one capabilities and seamless integration, offering a practical solution for streamlining hole preparation and finishing processes. Additionally, the unique feature of Combined CountersinkCounterbore Sets lies in their efficiency and precision, enabling users to optimize workflow and enhance machining accuracy effectively.
Key Features and Benefits of Keo Tools
Keo Tools offer a multitude of key features and benefits that set them apart in the industry. Precision engineering lies at the core of Keo Tools' superiority, ensuring top-notch performance and reliability. One key highlight is the micro-edge geometry, a defining characteristic that elevates the precision of tool operations. With advanced coating technologies, Keo Tools enhance durability and resistance to wear, extending their lifespan and usability. The strategic use of high-quality materials further underscores Keo Tools' reputation for excellence, ensuring consistent performance across various applications. Their exceptional heat and wear resistance make them a preferred choice for professionals seeking reliability and longevity. Moreover, Keo Tools boast versatility and adaptability, providing multi-purpose tools that offer customizable options to cater to diverse requirements.
Precision Engineering
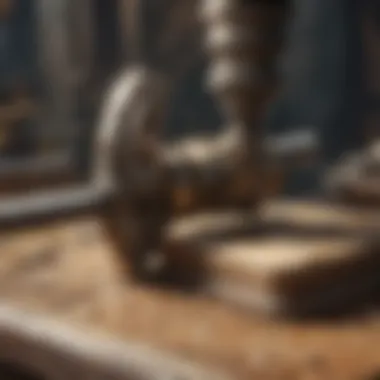
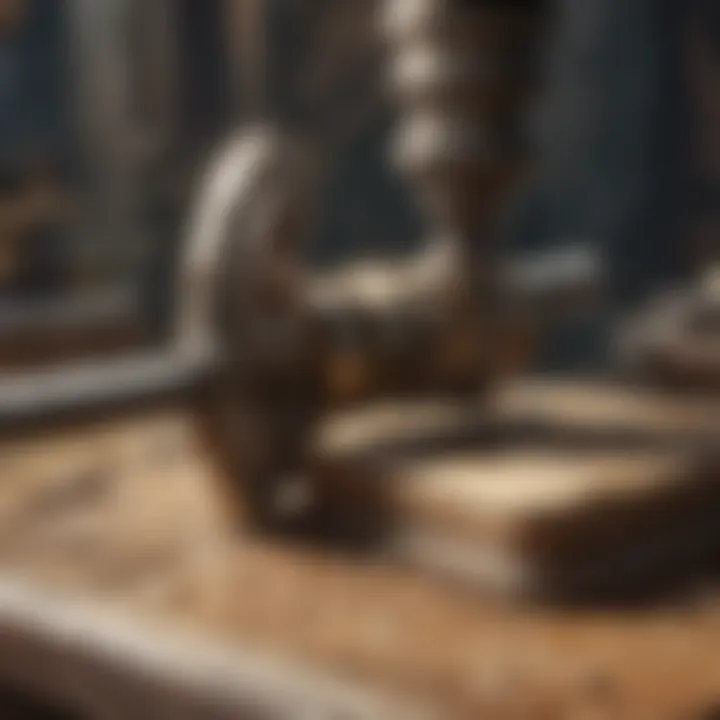
Micro-Edge Geometry
Micro-edge geometry is a critical aspect of Keo Tools' precision engineering. This feature enhances the cutting capabilities of the tools, enabling precise and intricate operations. The unique design of micro-edge geometry ensures superior cutting performance and promotes efficiency in various applications. Keo Tools leverage this characteristic to deliver exceptional results, making them a popular choice among professionals seeking accuracy and finesse. The advantages of micro-edge geometry are evident in its ability to produce high-quality finishes and achieve tight tolerances, elevating the overall performance of Keo Tools in demanding tasks.
Advanced Coating Technologies
The integration of advanced coating technologies reinforces Keo Tools' durability and efficiency. These coatings enhance tool resilience, reduce friction, and improve chip evacuation, leading to smoother cutting operations. The key characteristic of advanced coating technologies is their ability to prolong tool life and maintain sharpness during prolonged use. This feature makes Keo Tools a valuable asset in industrial settings where precision and endurance are paramount. While offering numerous benefits, including increased tool longevity, reduced tool wear, and enhanced performance, advanced coating technologies ensure that Keo Tools remain at the forefront of cutting-edge tool technology.
Durability and Longevity
High-Quality Materials
Keo Tools incorporate high-quality materials to guarantee exceptional durability and performance. The use of premium materials enhances the overall strength and reliability of the tools, contributing to their longevity and wear resistance. The key characteristic of high-quality materials in Keo Tools is their ability to withstand demanding conditions without compromising on cutting precision. This ensures that professionals can rely on Keo Tools for consistent and effective results across various tasks. Despite the advantages of high-quality materials, it is essential to consider potential limitations such as higher costs and specific maintenance requirements to maximize the benefits of these premium components.
Heat and Wear Resistance
Uncompromising heat and wear resistance are integral features of Keo Tools, ensuring optimal performance in challenging environments. The exceptional resistance to heat and wear guarantees that Keo Tools maintain their sharpness and durability even in high-temperature operations. The key characteristic of heat and wear resistance is its ability to prolong tool life and minimize the risk of premature wear, leading to cost savings and operational efficiency. While these features offer significant advantages in industrial settings where tool longevity is critical, it is important to handle Keo Tools with care to preserve their resistance properties and maximize their operational lifespan.
Versatility and Adaptability
Multi-Purpose Tools
Keo Tools deliver versatility and adaptability through their multi-purpose design, catering to a wide range of applications with ease. The key characteristic of multi-purpose tools is their ability to perform multiple functions, reducing the need for multiple tool types and enhancing workflow efficiency. This makes Keo Tools a preferred choice for professionals seeking versatility and convenience in their operations. The unique feature of multi-purpose tools lies in their customizable options, allowing users to tailor tool configurations to specific requirements, further enhancing their utility and adaptability. Despite the advantages of multi-purpose tools, it is important to assess the compatibility of customizations with intended applications to optimize tool performance and achieve desired results.
Customization Options
Customization options embedded in Keo Tools enable users to tailor tool specifications to suit their specific needs. The key characteristic of customization options is their flexibility, allowing users to modify tool features such as cutting angles, coatings, and materials. This bespoke approach enhances tool effectiveness in addressing diverse application scenarios, providing a personalized solution for professionals seeking customized tool solutions. While offering significant advantages in terms of versatility and adaptability, customization options require thorough consideration of operational requirements and compatibility factors to ensure optimal tool performance and user satisfaction.
Optimizing Performance with Keo Tools
Keo Tools are synonymous with precision and efficiency, emphasizing the critical role each tool plays in enhancing industrial processes. In this section, we delve into the key strategies for optimizing performance with Keo Tools to achieve superior results. Understanding the intricate balance between tool selection, material compatibility, speeds, and feeds is vital for maximizing the effectiveness of Keo Tools in various applications. By implementing best practices, users can significantly boost productivity and quality outcomes, setting a new benchmark in their operations.
Best Practices for Tool Selection
Matching Tools to Materials
When it comes to matching tools to materials, Keo Tools excels in providing a diverse range of options tailored to specific industrial needs. The accuracy and durability of cutting tools directly correlate with the material they are designed to work on. Keo Tools' meticulous attention to detail ensures that each tool is precisely engineered to handle various materials with optimal results. This seamless integration between tool and material elevates performance and minimizes errors, making Keo Tools a preferred choice for industries requiring unparalleled precision.
Considering Speeds and Feeds
The consideration of speeds and feeds is a fundamental aspect of tool selection that significantly impacts machining operations. Keo Tools' emphasis on optimizing speeds and feeds for different applications is a testament to their commitment to efficiency and quality. By fine-tuning the cutting speeds and feed rates according to the material and tool specifications, users can achieve exceptional surface finishes and extended tool life. This meticulous approach to speeds and feeds showcases Keo Tools' dedication to enhancing performance while prolonging tool longevity, a valuable combination in the competitive industrial landscape.
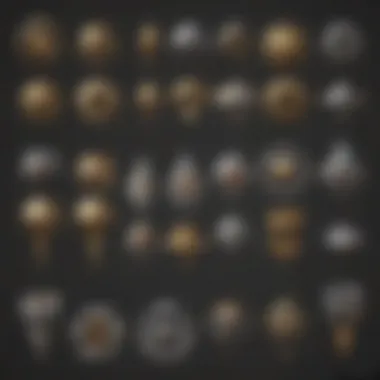
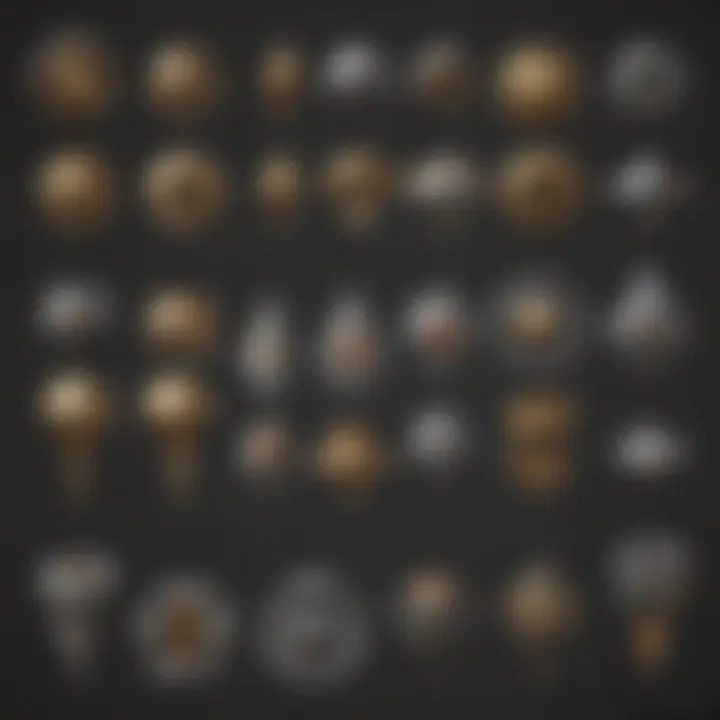
Maintenance and Care Tips
Cleaning and Storage Recommendations
Proper maintenance and storage of Keo Tools are essential for preserving their precision and functionality. The cleaning and storage recommendations provided by Keo Tools ensure longevity and sustained performance, safeguarding your investment in high-quality cutting tools. By following the recommended cleaning procedures and storing the tools in suitable conditions, users can extend the lifespan of their Keo Tools and maintain consistent cutting performance over time. This proactive approach to maintenance underscores Keo Tools' commitment to durability and customer satisfaction.
Sharpening and Refurbishing Guidance
As tools undergo wear and tear during use, sharpening and refurbishing become necessary to restore their original sharpness and effectiveness. Keo Tools' comprehensive guidance on sharpening techniques and refurbishing processes empowers users to prolong the lifespan of their tools without compromising on performance. The step-by-step instructions provided ensure that tools are sharpened accurately and refurbished to optimal condition, enabling users to maximize efficiency and cost-effectiveness. This focus on continuous tool maintenance exemplifies Keo Tools' dedication to supporting their customers in achieving long-term success.
Evolutionary Trends in Keo Tool Technology
In this section of the article, we delve into the Evolutionary Trends in Keo Tool Technology, a crucial aspect in understanding the progressive nature of these tools. Keo Tools has always been at the forefront of innovation, constantly evolving to meet the demands of modern industries. The incorporation of cutting-edge technology has propelled Keo Tools to new heights, setting them apart in the competitive market. By exploring the Evolutionary Trends, readers can gain insights into how technology plays a pivotal role in shaping the future of tool design and manufacturing.
Integration of IoT and Automation
Smart Tool Monitoring Systems
Smart Tool Monitoring Systems represent a significant advancement in tool utilization, leveraging IoT (Internet of Things) to enable real-time monitoring and analysis. These systems offer unparalleled visibility into tool performance, allowing for proactive maintenance and optimizing tool usage. The key characteristic of Smart Tool Monitoring Systems lies in their ability to collect and analyze data metrics, providing valuable insights for enhancing operational efficiency and productivity. This data-driven approach is a game-changer in the tool industry, offering precision and predictive maintenance strategies. While the advantages of Smart Tool Monitoring Systems are undeniable, challenges such as data security and system integration should be carefully considered to maximize their potential in industrial settings.
Automated Tool Change Solutions
On the other hand, Automated Tool Change Solutions revolutionize production processes by streamlining tool changeovers through automation. The key characteristic of Automated Tool Change Solutions is their efficiency in reducing downtime and increasing operational continuity. By implementing automated systems, companies can achieve higher throughput and consistent quality in manufacturing. The unique feature of Automated Tool Change Solutions lies in their adaptability to various machining environments, catering to a wide range of production setups. However, the implementation of automation requires thorough planning and integration to align with specific operational requirements effectively.
Advancements in Material Science
Nanostructured Coatings
Nanostructured Coatings present a breakthrough in material science, enhancing tool performance and longevity. The key characteristic of Nanostructured Coatings is their nano-thin film deposition, offering superior hardness and wear resistance. They are a popular choice for Keo Tools due to their ability to withstand demanding machining conditions and extend tool life significantly. The unique feature of Nanostructured Coatings is their capability to reduce friction and improve chip evacuation, contributing to enhanced machining precision. While Nanostructured Coatings bring immense benefits, considerations regarding application techniques and compatibility with different materials are essential for maximizing their advantages.
Composite Tool Compositions
On the other hand, Composite Tool Compositions introduce a versatile approach to tool design, combining different materials to create optimal tool performance. The key characteristic of Composite Tool Compositions is their tailored material blend, offering a balance of strength, toughness, and heat resistance. They are a beneficial choice for Keo Tools as they cater to diverse machining requirements with customized compositions. The unique feature of Composite Tool Compositions lies in their ability to optimize tool properties for specific applications, providing enhanced durability and productivity. However, understanding the interplay between different materials and their impact on machining processes is critical for leveraging the full potential of Composite Tool Compositions.
Future Prospects and Innovations in Keo Tool Design
In the ever-evolving realm of Keo tools, the segment on Future Prospects and Innovations plays a pivotal role in this comprehensive guide. Addressing the futuristic outlook of Keo tool design is essential for understanding the trajectory of these cutting-edge tools. By delving into upcoming advancements, industry professionals gain valuable insights into potential developments that could revolutionize the field. Investigating the potential improvements and innovations in Keo tool design not only broadens our understanding of current capabilities but also hints at what lies ahead for precision engineering and tooling solutions.
Enhanced Sustainability Practices
Keo Tools' commitment to sustainability shines through in their innovative approaches to tool design. Within this section, the focus is on Enhanced Sustainability Practices, emphasizing the importance of eco-conscious initiatives in tool manufacturing. One aspect under this umbrella is the incorporation of Recyclable Tool Components. These components are meticulously designed to be easily disassembled and recycled, minimizing environmental impact without compromising quality. Their eco-friendly nature contributes significantly to the overall goal of reducing waste and promoting a circular economy in the tooling industry.
Recyclable Tool Components
An in-depth exploration of Recyclable Tool Components reveals their instrumental role in promoting sustainability within the tooling sector. These components exhibit a unique characteristic of being easily separable and recyclable post-use, aligning with environmentally friendly practices. The distinct feature of Recyclable Tool Components lies in their ability to be repurposed without degradation in performance, making them a popular and responsible choice for environmentally conscious industries. The advantages of these components in minimizing ecological footprint and embracing a green approach to tool manufacturing cannot be overstated.
Energy-Efficient Production Techniques
Considering the significance of energy conservation in tool production, the discussion extends to Energy-Efficient Production Techniques. Highlighting the incorporation of energy-saving methods in Keo tool manufacturing, this segment underscores the efficacy of minimizing energy consumption throughout the production process. The key characteristic of these techniques is their ability to optimize resource utilization without compromising output quality. By adopting Energy-Efficient Production Techniques, Keo Tools not only reduce operational costs but also contribute to sustainable production practices in line with modern environmental standards. The advantages of such techniques in promoting energy efficiency and resource conservation are paramount for ensuring a greener and more sustainable future in tool design and manufacturing.